- May 26, 2017
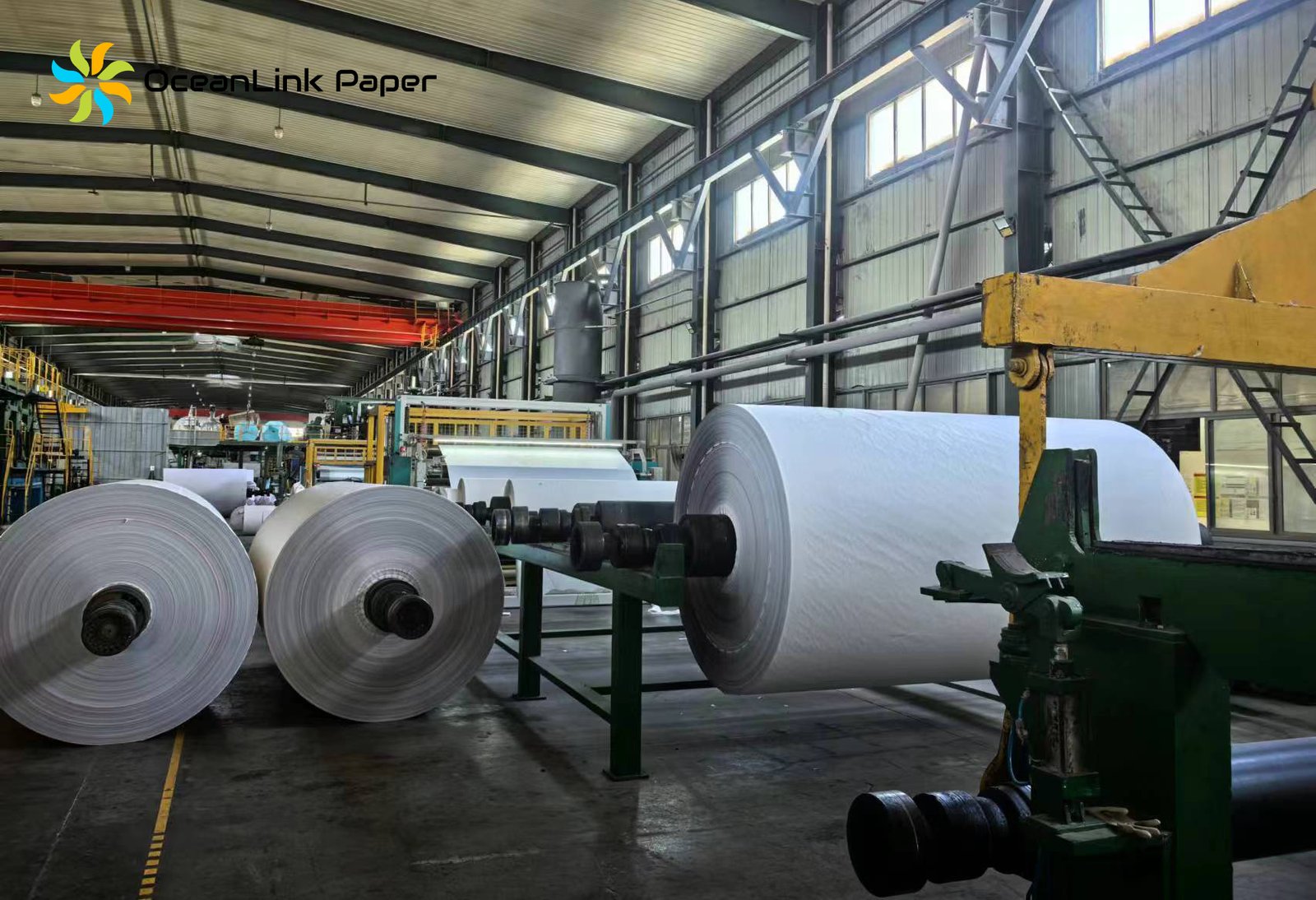
Printing tension fluctuations caused by web deformation can significantly impact the quality and efficiency of the printing process, particularly in continuous web printing applications such as flexography, gravure, and digital printing. Web deformation refers to changes in the shape, size, or position of the paper or film web during printing, which can lead to inconsistent tensions along the web path.
Causes of Web Deformation
Web deformation can be caused by various factors, including:
1. **Moisture Content Changes:** Paper and some types of film can absorb moisture from the environment or release moisture during the printing process, causing expansion or contraction.
2. **Temperature Variations:** Changes in temperature can alter the physical properties of the web material, leading to expansion or shrinkage.
3. **Mechanical Stress:** Tension variations, nip pressures, and other mechanical forces applied during printing can cause stretching or compression of the web.
4. **Roller Misalignment:** Misaligned rollers can cause the web to buckle or stretch unevenly, leading to tension fluctuations.
5. **Coating and Printing Processes:** Application of coatings or inks can add weight to the web, causing it to sag or deform, especially if the drying process is not controlled properly.
6. **Material Properties:** The inherent properties of the web material, such as stiffness, elasticity, and thickness uniformity, can contribute to deformation.
Impact on Printing Quality
Tension fluctuations due to web deformation can result in several printing defects, including:
– **Registration Errors:** Misalignment of printed images across different colors or layers.
– **Barreling and Coneing:** The web may form barrel-like or conical shapes, affecting the uniformity of ink distribution.
– **Wrinkling and Creasing:** The web may develop wrinkles or creases, leading to poor print quality.
– **Edge Curl:** The edges of the web may curl, which can cause problems in handling and feeding.
– **Print Density Variations:** Uneven tension can result in inconsistent pressure between the printing plate and the web, affecting ink transfer and print density.
Mitigation Strategies
To minimize the impact of web deformation on printing tension and quality, consider implementing the following strategies:
1. **Environmental Control:** Maintain stable temperature and humidity levels in the printing area to prevent moisture-related deformation.
2. **Preconditioning:** Allow the web material to acclimate to the printing environment before use to minimize moisture and temperature effects.
3. **Tension Control Systems:** Use advanced tension control systems that can adjust automatically to compensate for tension fluctuations.
4. **Regular Maintenance:** Ensure that all rollers and guides are properly aligned and maintained to avoid unnecessary stress on the web.
5. **Material Selection:** Choose web materials with better dimensional stability and appropriate mechanical properties for the printing process.
6. **Process Optimization:** Optimize printing parameters such as speed, tension, and nip pressures to match the characteristics of the web material.
7. **Training and Monitoring:** Train operators to recognize signs of web deformation and establish regular monitoring to catch issues early.
By addressing web deformation and its effects on printing tension, you can improve the overall quality and efficiency of the printing process, leading to reduced waste and increased productivity.